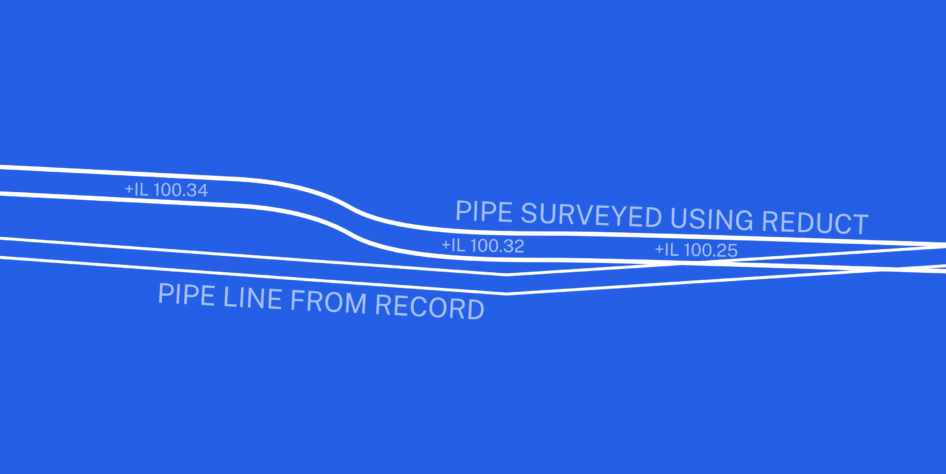
Gyroscopic mapping
Reduct is a unique, gyroscopic tunnel and pipeline mapping system which allows us to obtain accurate geospatial data of subsurface utilities on a site. This minimizes the risk of damage to existing infrastructure and helps our clients complete their projects safely and effectively.
The tool has several unique benefits. It can be used on any type of pipe material, including steel, in any utilities sector. The autonomous logging system means there’s no need to trace the probe as it travels through the pipe. And it can be used near live power lines and railways as it causes no electromagnetic interference.
The data recorded by the Reduct tool is presented as a highly accurate 3D alignment of the pipe length that has been mapped.
Frequently Asked Questions
In what situations can gyroscopic mapping be an effective solution?
Gyroscopic mapping can be used effectively for mapping sewers/pipes in underground environments where access above the line is not possible or easy such as under buildings, railways or bodies of water.
The device accuracy is independent of depth and immune to outside interference and so is more accurate than a sonde when these factors apply.
Gyroscopic mapping can be used in confined or hazardous spaces which are too difficult or unsuitable for a conventional survey. It is also useful and effective in complex pipes to record bends and changes in gradient.
Places where a gyro could be deployed include:
- Sewers
- Water main
- Gas pipe
- Duct
- QA on horizontal directional drilling (HDD)
How is the collected data used to generate a map or model of the pipeline?
The Reduct gyroscopic tool will accurately measure the X, Y, Z co-ordinates along a route when provided with the start and finish co-ordinates. Specialist software will provide the QA analysis, calculate the mean position from multiple runs and export the results as a CSV file.
This can then be manipulated and presented in CAD or GIS software and if geo-referenced this could be shown against a topographical or utility survey background.
How accurate is gyroscopic mapping, and what factors can affect the precision of the results?
Gyroscopic mapping can be affected by the following factors:
Calibration Gyroscopic instrumentation should be regularly calibrated by the manufacturer. This also allows software updates which could improve the results of the data.
Quality of the starting coordinates Any error in start and end co-ordinates will be introduced into the results.
Knowledge of the equipment and its proper use Gyroscopic equipment is most accurate when used by trained and competent staff who know how the equipment works and how to get the best results.
Condition of the pipe This can affect the accuracy of the gyroscopic data. The pipe may require cleaning of silt and debris to ensure the device can travel through it smoothly. Gyroscopes don’t like sudden jolts that affect the accuracy of the data.
In good conditions using a centralising wheelset the accuracy of a 400m long pipe would be expected to be within +/-40cm in plan and 20cm in level.
What are the main advantages of gyroscopic mapping over traditional pipeline mapping methods (e.g., person entry, sonde) and how does this contribute to safety?
The main advantages of gyroscopic mapping over that of traditional pipeline mapping is that it removes the need for access above the utility of interest, such as under buildings, rivers, railways and roads or other hazardous locations.
Additionally, the use of gyroscopic devices reduces or removes the need for confined space access. Staff do not need to survey along the tunnel or pipe to complete the survey.
Gyroscopic surveys are not dependant on depth whereas sondes are limited to 5-10m.
The Gyroscopic device is not subject to external interference such as electricity cables that effect a sonde.
The gyroscopic data can be downloaded and analysed on site ensuring that it is within acceptable tolerances before leaving site. Repeat work is therefore avoided.
The gyroscopic instrument constantly records data as it moves through the pipeline/sewer, as such, it is better able to map out curves’, gradients and bends in the pipe than a traditional sonde or man entry method.